Watch the FREE webinar (duration 2 hours 15 min.) covering various aspects of the geopolymer science with real world applications, including a special focus on geopolymer cement and concrete to celebrate its successful commercialization.
A recent Technical Paper #24 denounces the false values on CO2 emission published in several scientific papers. See at “False CO2 values published in scientific papers“.
Geopolymer cement is often mixed up with alkali-activated slag. The later was developed since 1956 in the former USSR (now Ukraine) by G.V. Glukhovsky. Alkali-activation, which is generally performed with corrosive chemicals (see below User-friendly), is used for the making of concretes exclusively. The alkali-activated materials are not manufactured separately and not sold to third parties as commercial cements. On the opposite, geopolymer technology was from the start aimed at manufacturing binders and cements for various types of applications.
A video stresses the major differences between alkali-activated materials/alkali-activated construction materials and geopolymers, go to “Why Alkali-Activated Materials are NOT Geopolymers?“
For detailed information on Fly Ash based Geopolymer Cements and Concretes see in the Library the Technical paper #22 at GEOASH: fly ash-based geopolymer cements as well as the recently updated book Geopolymer Chemistry & Applications, Chapters 12, 24 and 25, and the results of the European Research project GEOASH in the next section. You may also go to the Geopolymer Library and download several papers, for example #21 Geopolymer cement review 2013, #22 GEOASH, #23 GP-AIRPORT.
In this section we are developing:
a) The recent industrial development of geopolymer concrete (100,000 tonnes and +)
b) The User-friendly geopolymer cement concept.
100,000 tonnes of Geopolymer Concrete for Airport + Eco-building
Brisbane West Wellcamp Airport (BWWA), Toowoomba, Queensland, is Australia’s first greenfield public airport to be built in 48 years. BWWA became fully operational with commercial flights operated by Qantas Link in November 2014. See our News dated of October 14, 2014, 70,000 tonnes Geopolymer Concrete for airport.
This project marks a very significant milestone in engineering – the world’s largest geopolymer concrete project. BWWA was built with approximately 40,000 m3 (100,000 tonnes) of geopolymer concrete making it the largest application of this new class of concrete in the world. The geopolymer concrete developed by the company Wagners, known as Earth Friendly Concrete (EFC), was found to be well suited for this construction method due to its high flexural tensile strength, low shrinkage and workability characteristics. Heavy duty geopolymer concrete, 435 mm thick, used for the turning node, apron and taxiway aircraft pavements, welcomes a heavy 747 cargo for regular air traffic between Toowoomba-Wellcamp BWWA airport and Hong Kong. For technical details read the paper by Glasby et al. (2015), EFC Geopolymer Concrete Aircraft Pavements at Brisbane West Wellcamp Airport, in our Library, Technical paper #23 GP-AIRPORT. Technical Paper on Geopolymer Aircraft Pavement.
Prof. Joseph Davidovits’ visit to the Toowoomba-Wellcamp-Airport.
On October 3, 2015, Joseph and Ralph Davidovits flew from Sydney Airport to Toowoomba-Wellcamp-Airport, for a visit to the company Wagners.
Prof. Joseph Davidovits’ visit to the Global Change Institute, Brisbane, Queensland, Australia.
On October 7, 2015, Joseph and Ralph Davidovits drove with Tom Glasby and Russell Genrich, company Wagners, from Toowoomba to Brisbane. Our News dated December 10, 2013, was titled World’s first public building with structural Geopolymer Concrete. It introduced the world’s first building to successfully use geopolymer concrete for structural purposes, the Global Change Institute, University of Queensland, Brisbane, Queensland, Australia. The 4 story high building, for general public use, comprises 3 suspended geopolymer concrete floors involving 33 precast panels. They are made from slag/fly ash-based geopolymer concrete coined Earth Friendly Concrete (EFC), a Wagners brand name for their commercial form of geopolymer concrete.
Mass Production of Geopolymer Cement
At the Geopolymer Camp 2009 at Saint-Quentin, France, Prof. Joseph Davidovits presented a keynote on “Practical Problems on Mass Produced Geopolymer Cement”. What are the key issues and what are the dead ends? What to do to make a cement that reduces the CO2 emission by 60 up to 80%?
J. Davidovits’ Keynotes at Geopolymer Camp 2010, 2011, 2012, 2013, 2014 and 2015 contain additional information. Go to Keynotes of the Geopolymer Camp.
In the recently updated book Geopolymer Chemistry & Applications several chapters are dedicated to geopolymer , metakaolin-based, rock-based and fly ash-based cements and concretes, see in Chapters 8, 9, 10, 11, 12, 24 and 25. You may also go to the Geopolymer Library and download several papers.
If we compare in a microscope the structure of mortar made of regular cement with another sample made of geopolymer, we notice that the regular cement is a coarse stacking of grains of matter. This causes cracks and weaknesses. On the opposite, geopolymer cement (in black) is smooth and homogeneous. This provides, in fact, superior properties.
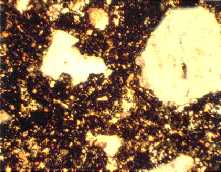
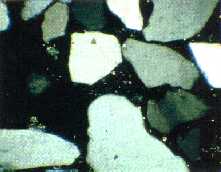
User-friendly geopolymer cements
Although geopolymerization does not rely on toxic organic solvents but only on water, it needs chemical ingredients that may be dangerous and therefore requires some safety procedures. Material Safety rules classify the alkaline products in two categories:
- corrosive products
- irritant products
The two classes are recognizable through their respective logos displayed below.
The Table lists some alkaline chemicals and their corresponding safety label. The corrosive products must be handled with gloves, glasses and masks. They are User-hostile and cannot be implemented in mass applications without the appropriate safety procedures. In the second category one finds Portland cement or hydrated lime, typical mass products. Geopolymeric mixes belonging to this class may also be termed as User-friendly.
When, in 1983 at the Central Laboratory of the American company Lone Star Industries, we started the research on geopolymer cements (Pyrament cement), we decided to select alkaline conditions that are User-friendly. (Na,K,Ca)-Poly(sialate-siloxo) and K-Poly(sialate) products (resins, binders and cements) have starting molar ratio SiO2:M2O ranging from 1.45 to 1.85. Unfortunately, this is not followed by other scientists and technicians involved in the development of so-called alkali-activated-cements, especially those based on fly ashes, with molar ratio in average below 1.0. Looking only at low-costs consideration, not at safety and User-friendly issues, they propose systems based on pure NaOH (8M or 12M). For example in a “State of the Art” on alkali-activated fly-ash cements, wrongly named geopolymer technology, published in 2007, several scientists claimed that the pure NaOH system should be considered as the reference for fly-ash-based cements (see: Duxson P., Fernandez-Jimenez A., Provis J.L., Lukey G.C., Palomo A. and van Deventer J.S.J., Geopolymer technology: the current state of the art, J. Mater. Sci., 42, 2917-2933, 2007). These are User-hostile conditions for the ordinary labor force employed in the field.
Finally, companies refuse to support the liability and pay high insurance fees based on such out-of-date processes. Indeed, laws, regulations, and state directives push to enforce for more health protections and security protocols for workers’ safety. Further details on fly-ash-based geopolymer cement in the page GEOASH, a project aimed to develop a real industrial process driven by these constraints.